|

The PepsiCo factory was opened in the Moscow region today. They will produce Aqua Minerale drinking water, Lipton Ice Tea, Adrenaline Rush power drinks, etc. As soon as the factory starts producing 2,1 billion liters a year, it will be considered the largest PepsiCo enterprise in Europe and the second largest enterprise of the company in the world.
Pepsi company came to Russia in July 1959 when the first American national exhibition was organized in Moscow. On that day Vice-President of the USA Richard Nixon who was in the head of the American delegation invited Nikita Khrushchev to have a glass of Pepsi and First Secretary of the Communist Party of the Soviet Union did so with pleasure. That time Pepsi slogan said: Be Sociable, Drink Pepsi. World newspapers typed photos of Mr. Khrushchev stressing: Khrushchev is learning to be sociable.

But the agreement on selling Pepsi-Cola in the USSR was concluded 10 years later. Instead the USA agreed to import Russian vodka Stolichnaya. In 1979 Pepsi Cola was widely available in Moscow. By the way, water that forms the basis of all the drinks at the factory gets pured in the hall.

In 1992 the first Pepsi production line was opened in Saint-Petersburg increasing production volume twice. In 1992 Coca-Cola company announced their plans to construct a plant that will be engaged in Pepsin manufacturing. By that time the main competitor of Coca-Cola named PepsiCo company was an active member of the Russian market. Today the latter owns 9 factories in Russia.

Table of water chemical control.

Plastic bottles are made here as well. The first Pepsi bottle appeared in the USA market in 1970. In Russia PET-bottles were exported till 1997 and today they are produced at the local factory.

A case with bottles is sent to conveyor.

Warm PET-bottles are put into a blowing unit. A stock is installed inside a bottle which spreads it to sides. Compressed air enters the mold turning it into a real bottle. The package can provide for safe storage of water and alcohol-free drinks during 1,5-12 years depending on the storage conditions. By the way, the thinner the wall depth of the bottles is, the longer it serves.


Bad bottles are discarded.


Here water is mixed with syrups.

Ready-made drinks are poured into bottles.
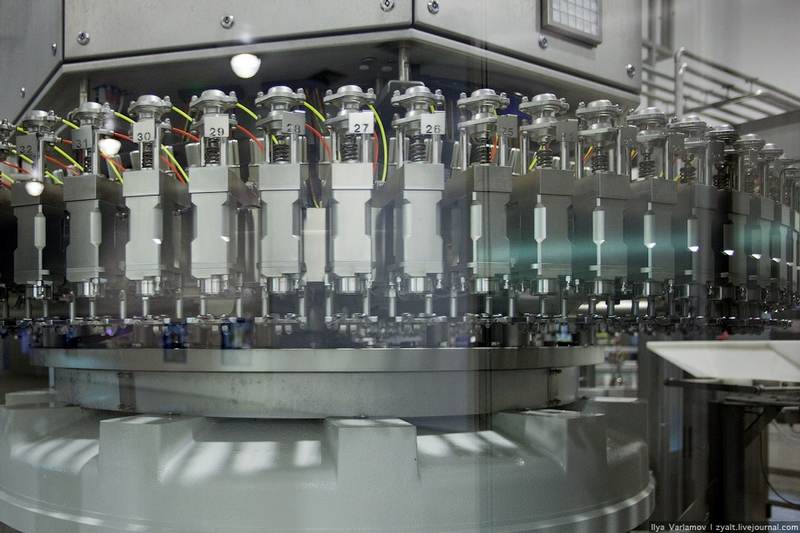
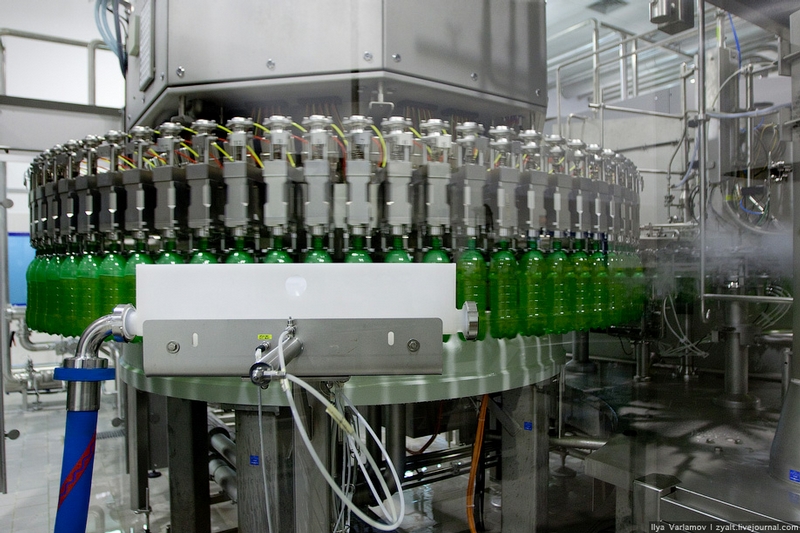
The process is very fast.
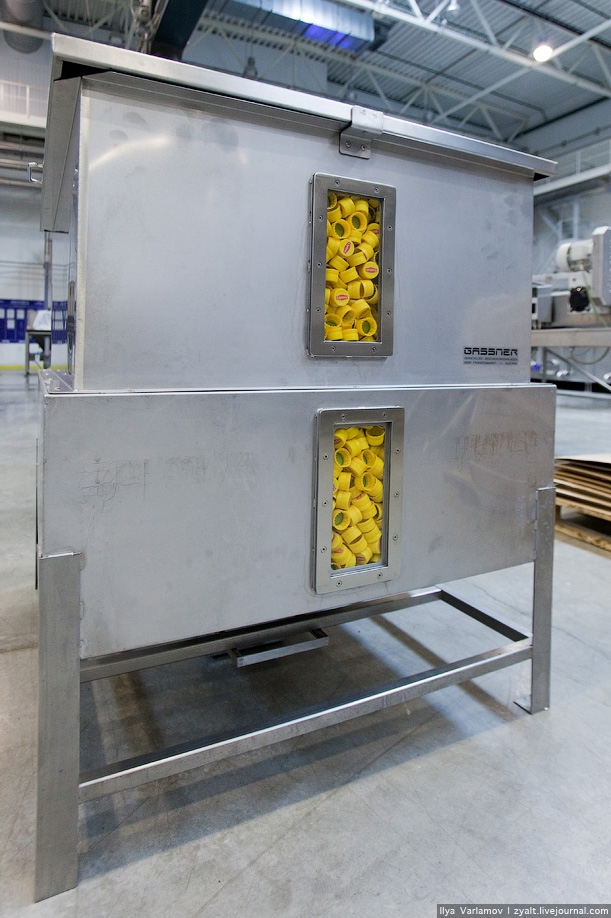
Caps are waiting for their turn.
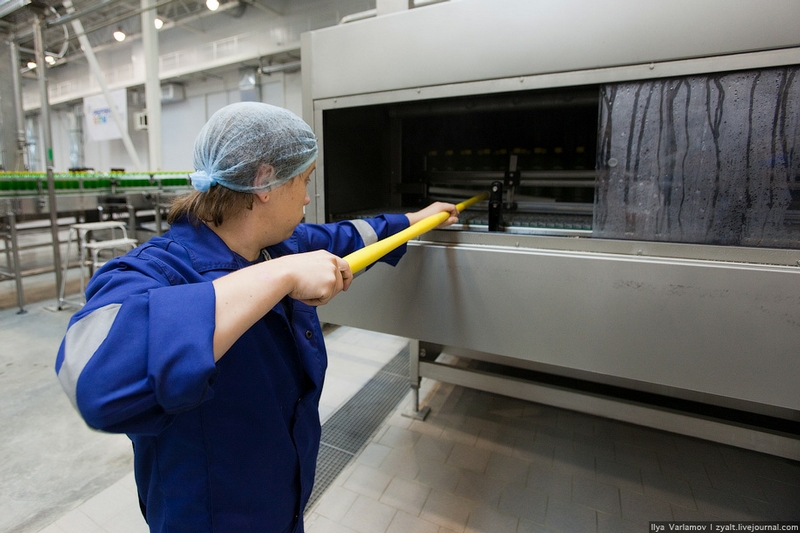
One of several manual operations. The bottles are sent to temperature tests. They are first cooled down and then heated to 80 degrees Celsius. At the stage a part of bottles gets discarded.
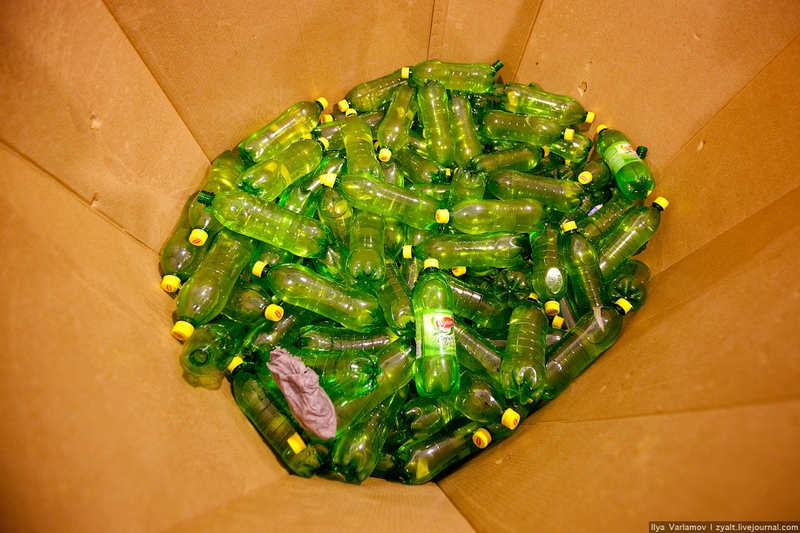
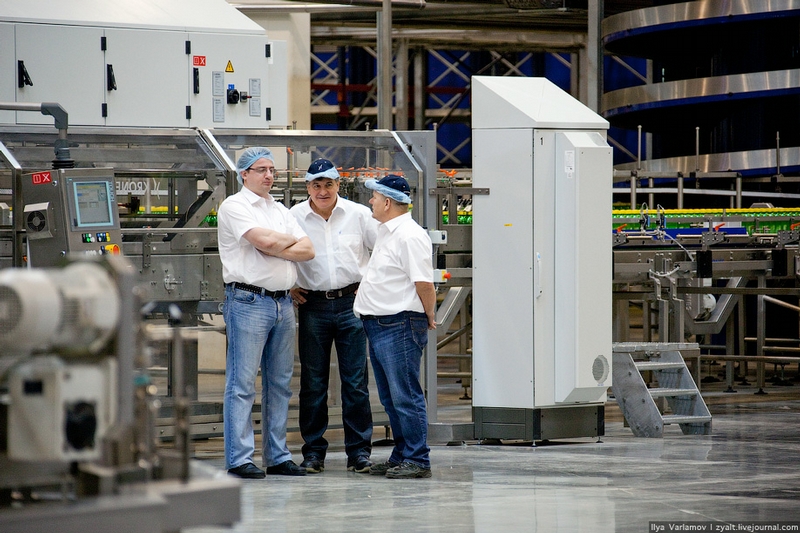
The production is almost completely automatized with the exception of several operations. The employers have only to control it.
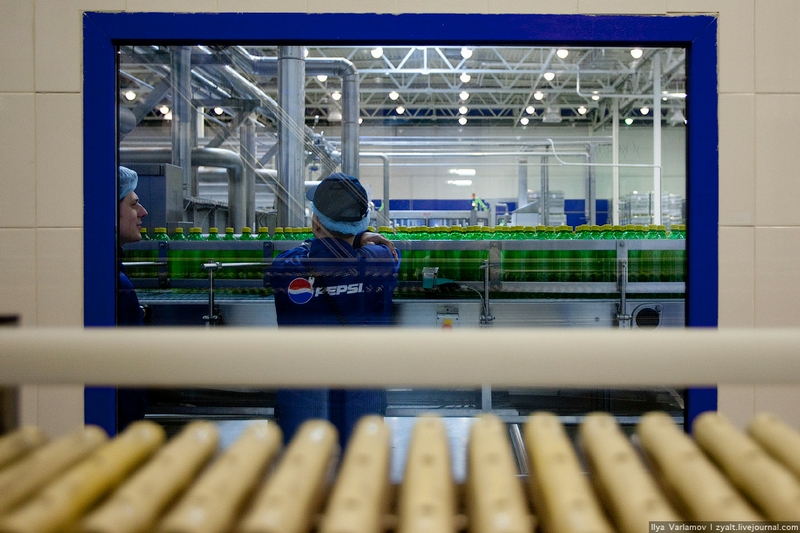
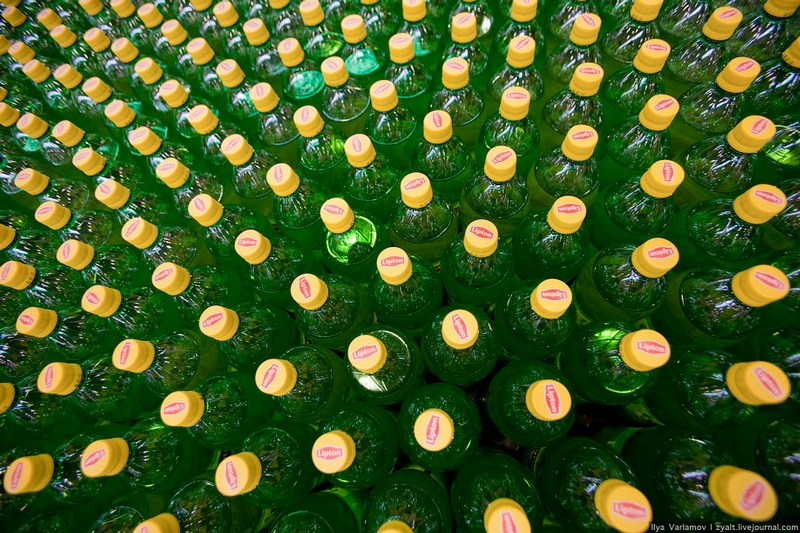
And now tested bottles are ready to reach their consumers.
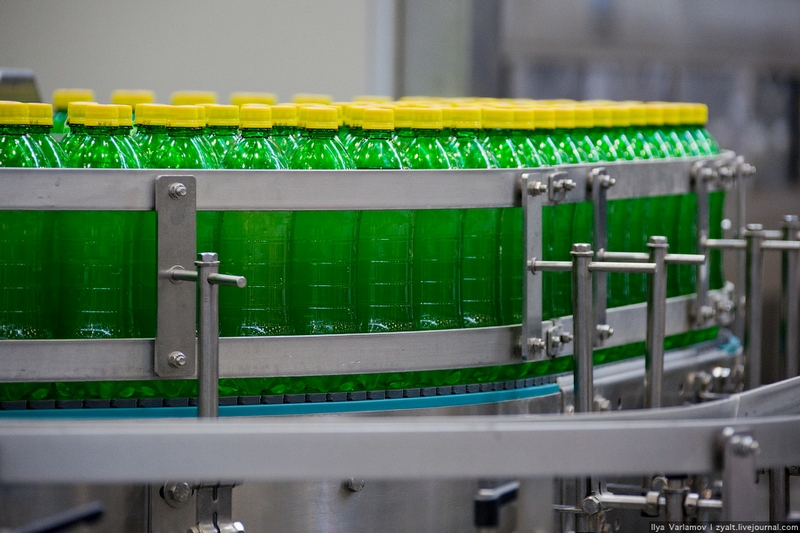
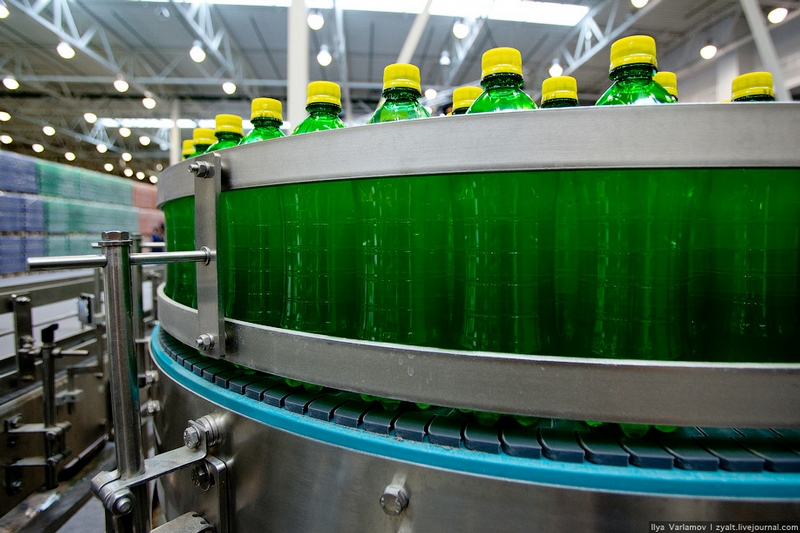
Workers look through the glass if the labels are of good quality.
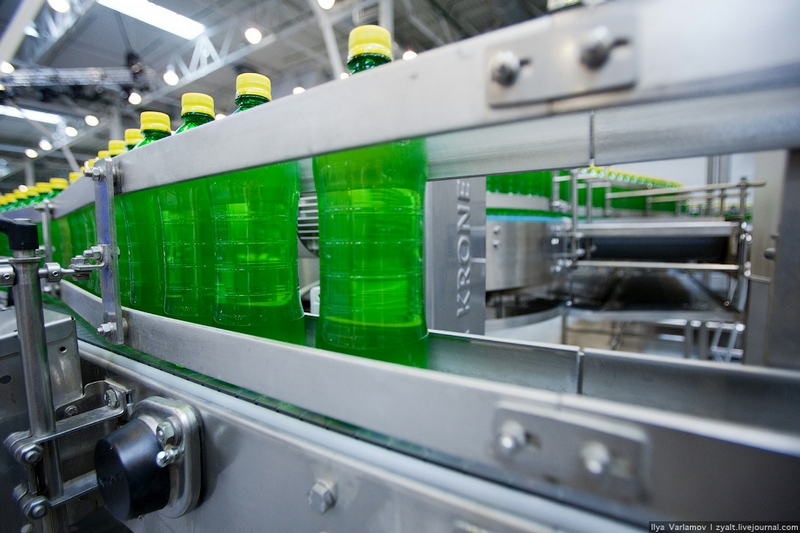
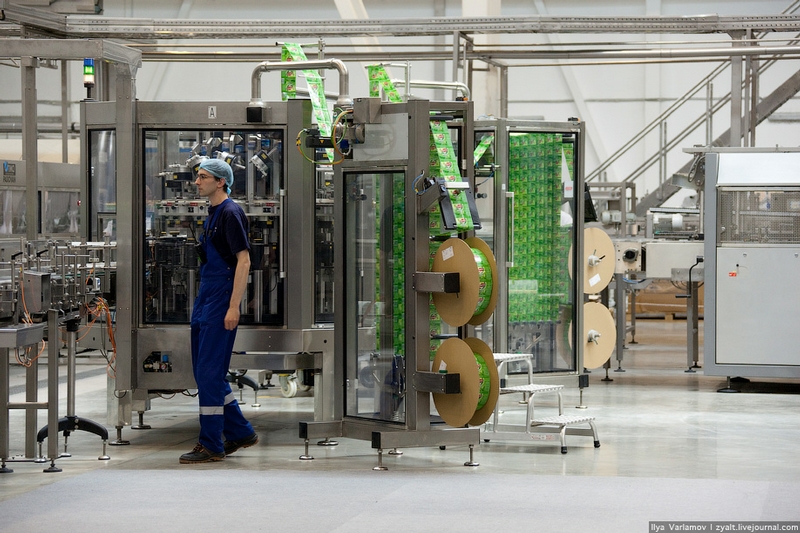
But before a label must be made which is realized with a special machine.
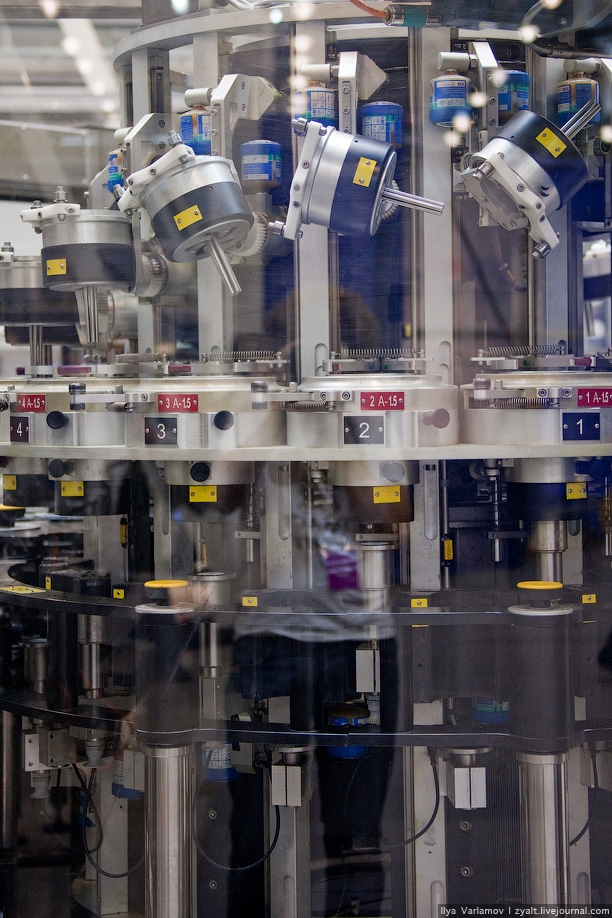
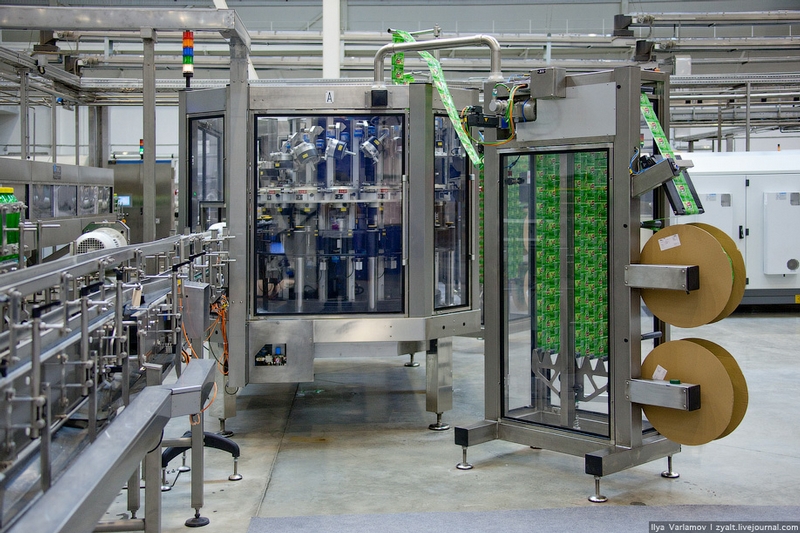
Nobody sticks the label today. It is fused instead.
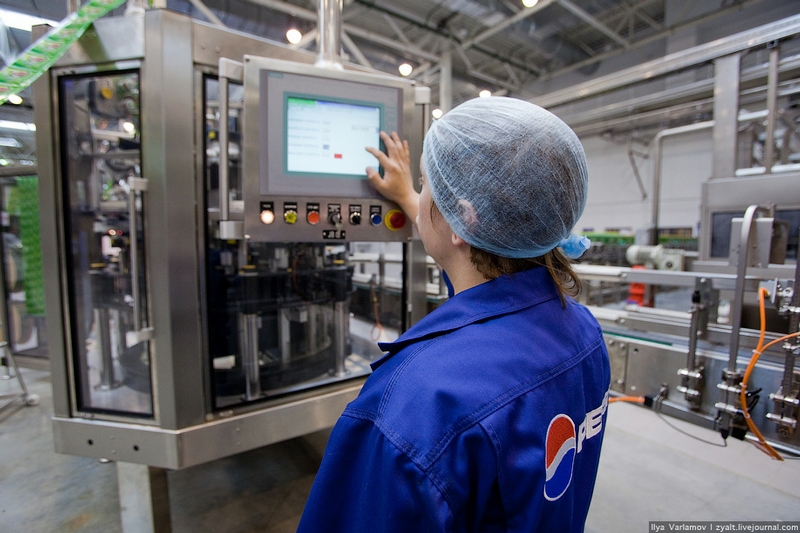
Bad types of labels are chosen by a robot and put into a special case.
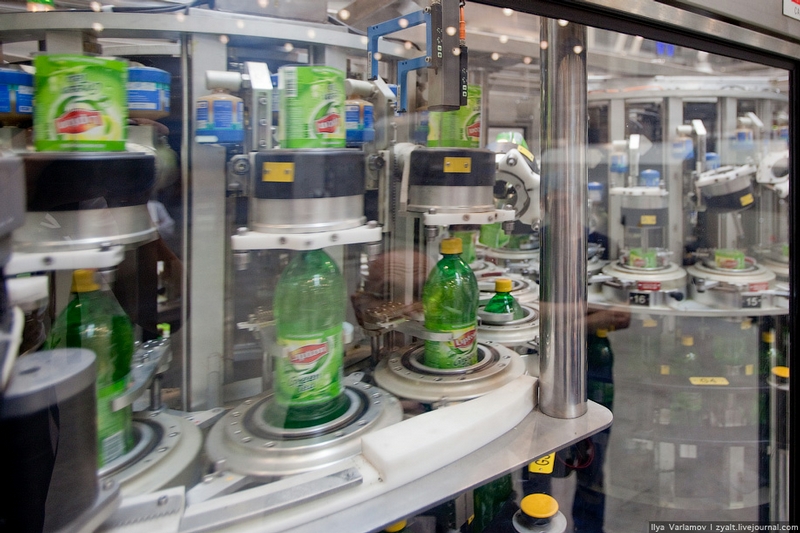
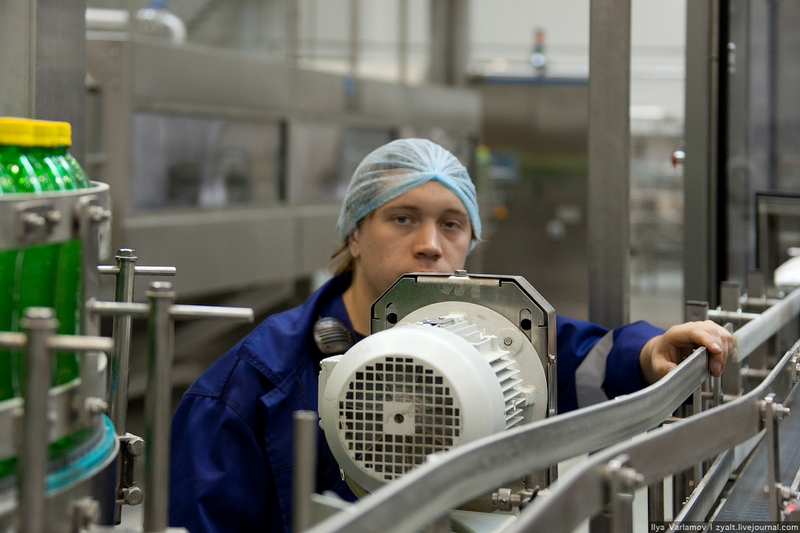
12 bottles are put together.
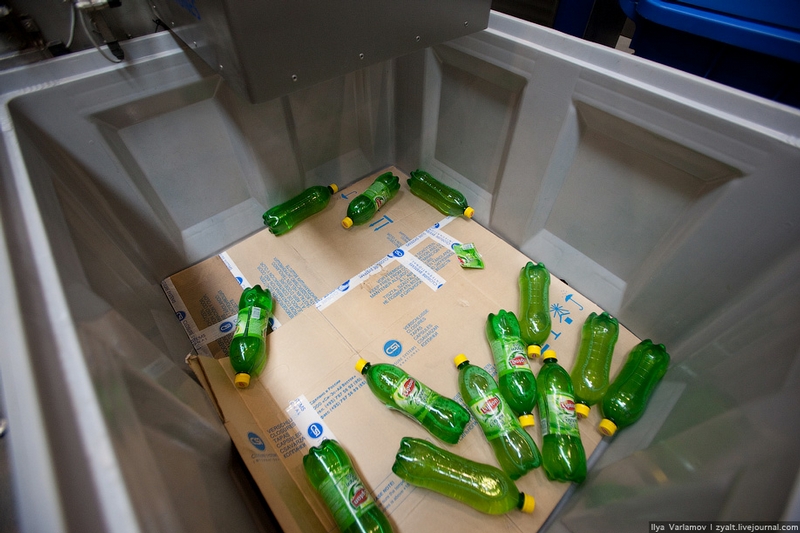
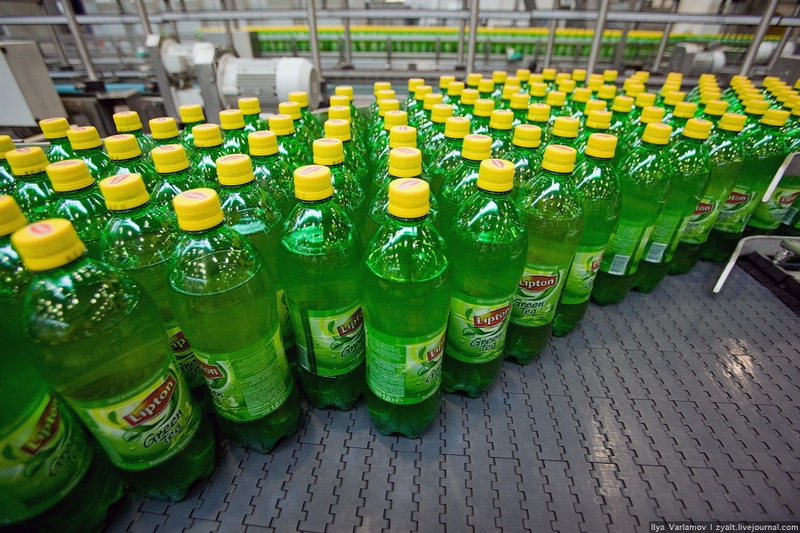
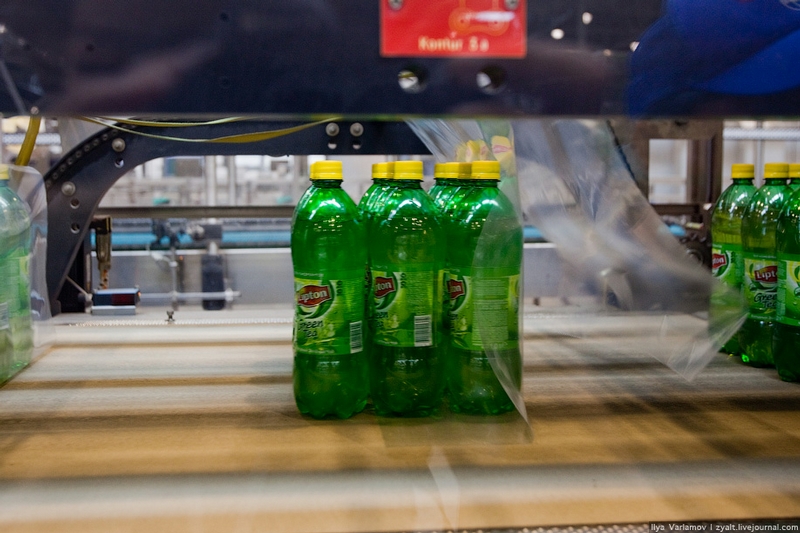
They are fused with hot air.
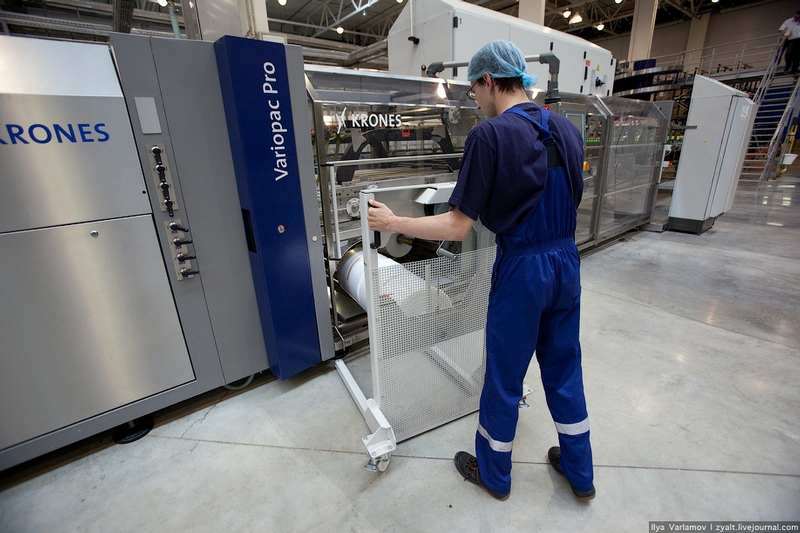

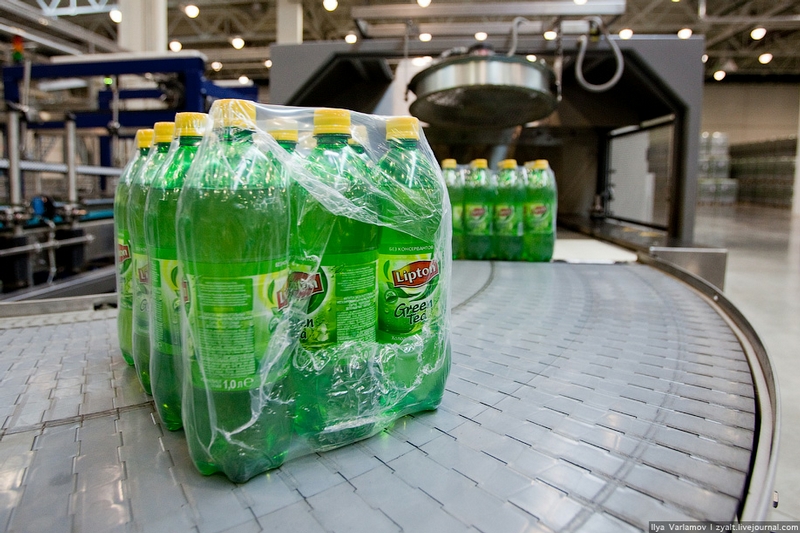
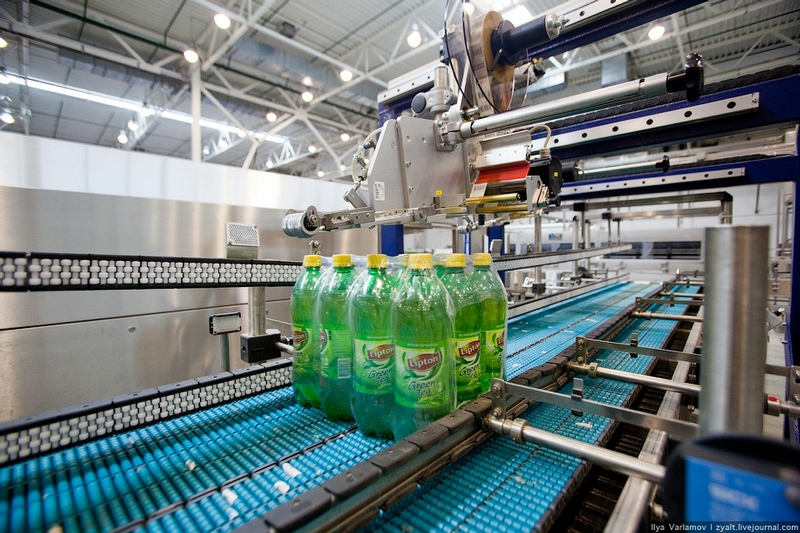

A code is applied to the bottle. Then it goes to the adjacent hall.
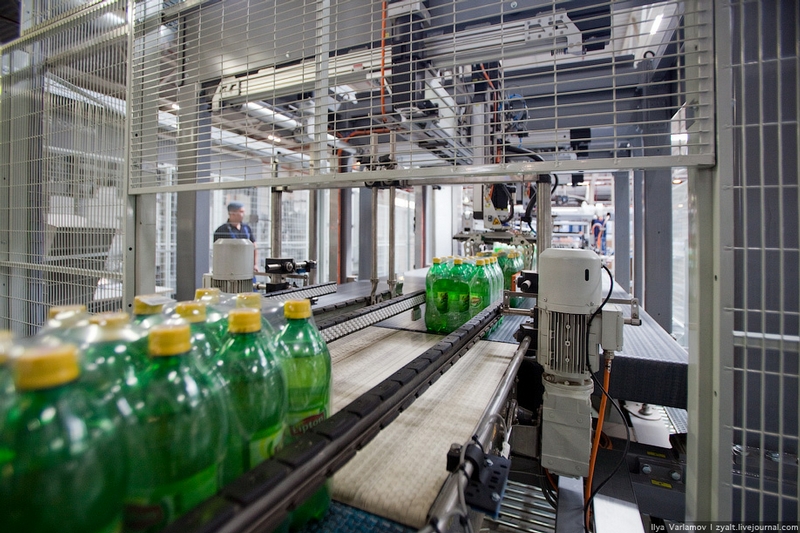
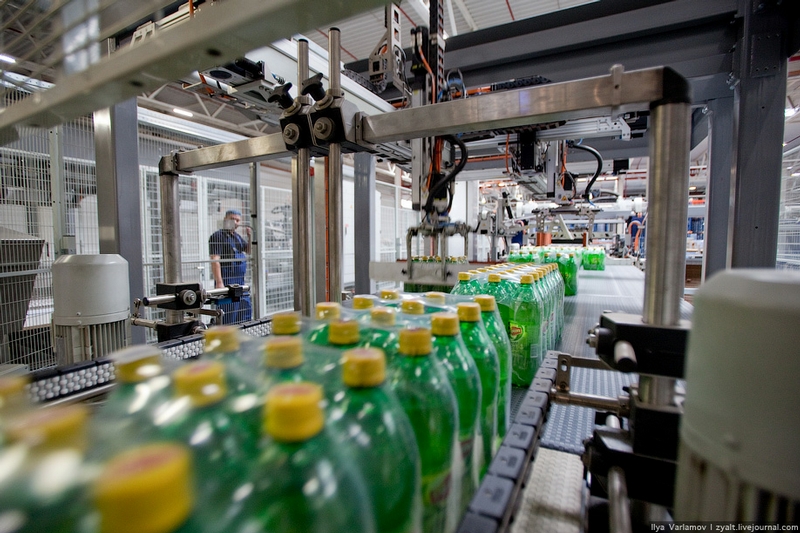
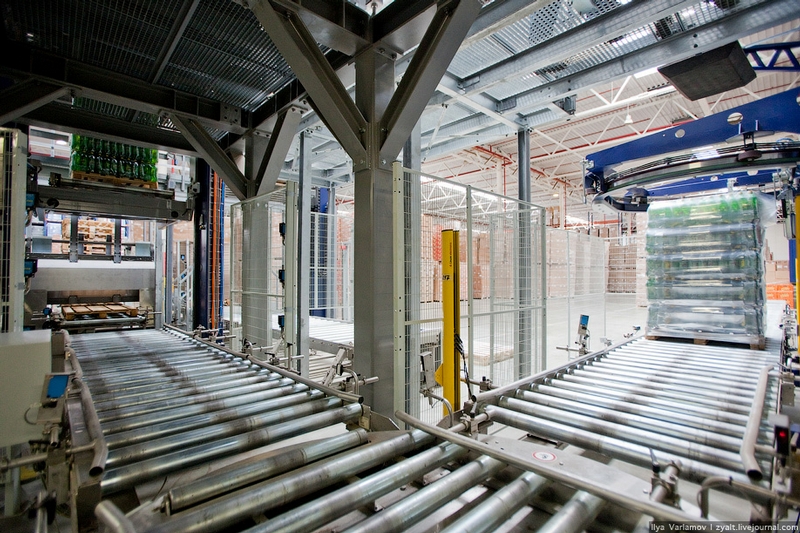
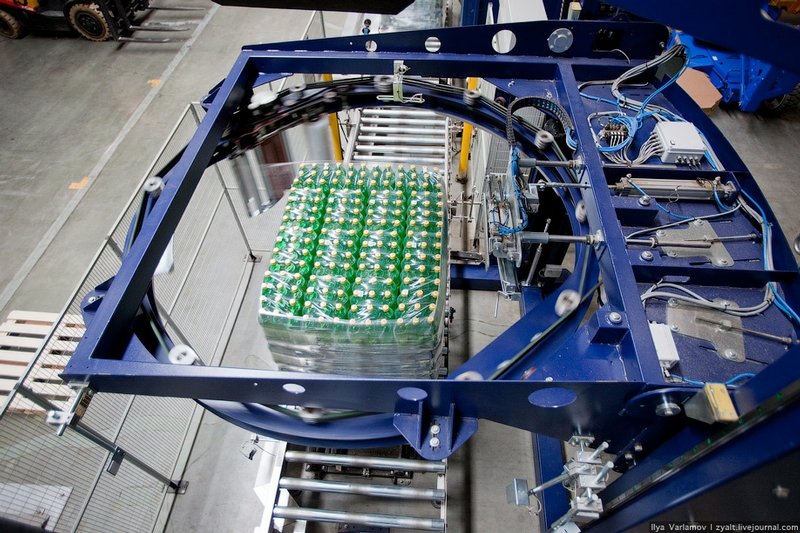
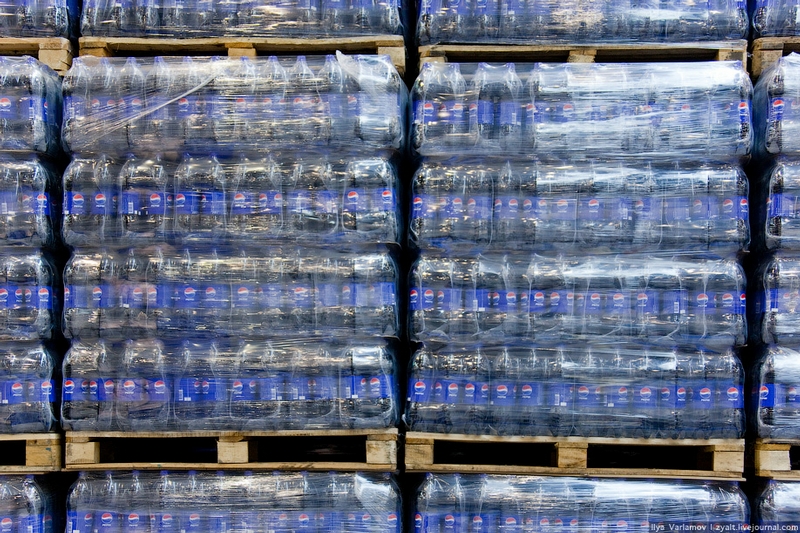
The bottles are wrapped into a film. This is how the bottles look when they reach the warehouse from where they go to consumers.
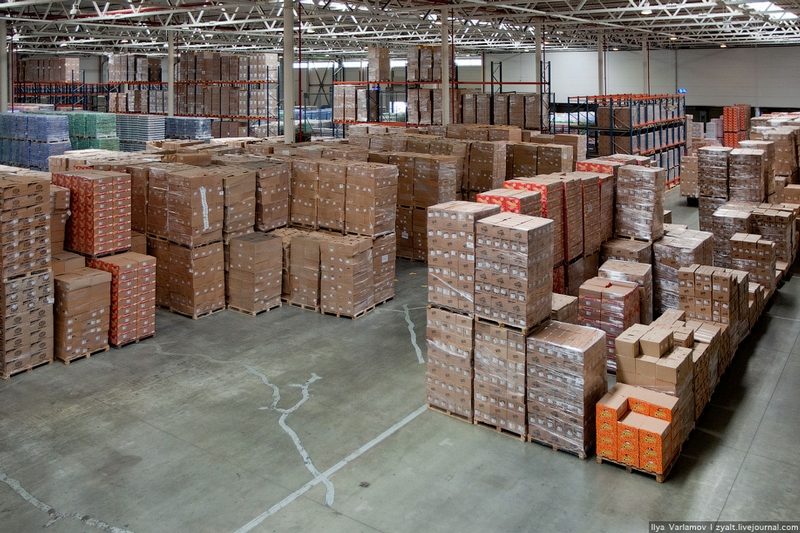
|
Rate
-
1
View Rating Log
-
|
|
|
|
|
|
|
terima kasih TT karena i dapat melawat kelang atas sesawang on line |
|
|
|
|
|
|
|
wow...baru tau suasana kilang dia |
|
|
|
|
|
|
|
waaa..lawatan sambil belajar kelas anggur ke kilang pepsi  |
|
|
|
|
|
|
|
menarik infor..  |
|
|
|
|
|
|
|
Pengunaan mesin sepenuhnya kilang pun nampak bersih dengan pengunaan tenaga manusia ditahap yang paling minimal. |
|
|
|
|
|
|
| |
|